The Economics of Lithium Battery Production and Supply Chains
Lithium batteries have become integral to our modern lives, powering everything from smartphones and laptops to electric vehicles and renewable energy storage systems. Understanding the economics of lithium battery production and its intricate supply chains becomes crucial as the world continues to embrace clean energy solutions and the demand for electric vehicles rises. This article will delve into the various aspects of lithium battery economics, including production costs, supply chain complexities, key players, and future prospects.
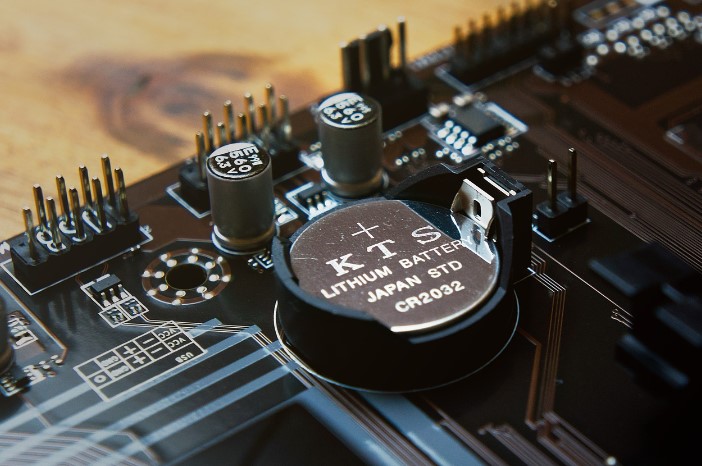
The Importance of Lithium Batteries
Lithium batteries have become indispensable in our daily lives due to their numerous advantages. Lithium batteries offer higher energy density, longer lifespan, and faster charging capabilities than traditional lead-acid batteries. These factors have made them the preferred choice for portable electronic devices like smartphones and laptops.
Additionally, lithium batteries have emerged as a game-changer in the transportation sector. Advancements in lithium battery technology have driven mainly the global shift towards electric vehicles (EVs). EVs powered by lithium batteries offer more excellent range, reduced emissions, and lower operating costs than conventional internal combustion engine vehicles. Check out https://goldenmateenergy.com/Â
Economics of Lithium Battery Production
Global Demand and Market Growth
The demand for lithium batteries has been soaring in recent years. The market for lithium-ion batteries alone is expected to reach billions of dollars by [current year + 5]. The growing adoption of electric vehicles, grid-scale energy storage systems, and portable electronic devices have driven this exponential growth.
Cost of Raw Materials
Lithium-ion batteries comprise various raw materials, including lithium, cobalt, nickel, and graphite. The cost and availability of these materials significantly impact the economics of lithium battery production. Fluctuations in the prices of these raw materials can profoundly affect the overall production costs.
Manufacturing and Labor Costs
The manufacturing process of lithium batteries involves multiple stages, including electrode fabrication, cell assembly, and battery pack integration. Labor costs, automation, and economies of scale are crucial in determining manufacturing costs. Battery manufacturers constantly strive to optimize production processes to improve efficiency and reduce costs.
Key Players in the Lithium Battery Industry
The lithium battery industry comprises several key players involved in different supply chain stages. Understanding the roles of these players is essential to comprehend the economics of lithium battery production. Added to that, you can also learn how to hookup a din rail power supply and other power supply solutions.
Battery Manufacturers
Battery manufacturers are responsible for producing lithium-ion cells and battery packs. These companies invest heavily in research and development to improve battery performance and reduce costs. Major manufacturers such as Tesla, LG Chem, and Panasonic dominate the industry and have established extensive production facilities worldwide.
Suppliers of Raw Materials
Raw materials suppliers, including lithium, cobalt, nickel, and graphite, play a critical role in the lithium battery supply chain. These suppliers must ensure a consistent supply of high-quality materials at competitive prices. Fluctuations in material prices and availability can cascade effects on battery production costs.
Battery Pack Assemblers
Battery pack assemblers are responsible for integrating lithium-ion cells into battery packs. These companies often work closely with manufacturers to design and assemble battery packs according to specific customer requirements. They play a crucial role in optimizing lithium batteries’ packaging and thermal management.
Global Supply Chains
Lithium battery production and supply chains are complex and involve multiple stages spanning different countries and continents.
Extraction and Processing of Lithium
Lithium is primarily extracted from lithium-rich brine or hard rock deposits. Major lithium-producing countries include Australia, Chile, and China. After extraction, lithium undergoes several refining processes to obtain high-purity lithium compounds suitable for battery production.
Battery Component Production
Producing battery components like cathodes, anodes, and electrolytes is a global affair. Different countries specialize in different parts. For example, China dominates the production of cathode materials, while Japan leads in anode production. This global distribution of component production helps optimize costs and ensure a reliable supply chain.
Battery Assembly and Distribution
Battery assembly involves the integration of lithium-ion cells into battery packs. This process often occurs near the end markets to minimize transportation costs and improve logistics efficiency. Finished battery packs are distributed worldwide to manufacturers of electric vehicles, consumer electronics, and energy storage systems.
Challenges and Risks in the Lithium Battery Supply Chain
Despite the lithium battery industry’s rapid growth and potential, its supply chain has various challenges and risks.
Supply and Demand Imbalances
The electric vehicle market and the renewable energy sector heavily influence the demand for lithium batteries. Fluctuations in demand and supply imbalances can lead to price volatility and affect the stability of the supply chain.
Political and Geographical Risks
Lithium reserves are concentrated in a few countries, and these regions’ geopolitical tensions or policy changes can disrupt the supply chain. Moreover, transporting lithium and other raw materials over long distances poses logistical challenges and increases the risk of delays or disruptions.
Environmental Concerns
Lithium battery production has environmental implications, including the extraction and processing of lithium, the disposal of spent batteries, and the energy-intensive manufacturing processes. Sustainable practices and recycling initiatives are vital to mitigate these environmental concerns.
Strategies for Optimizing Lithium Battery Supply Chains
Various strategies can be implemented to overcome the challenges and risks associated with lithium battery supply chains.
Diversification of Suppliers
Battery manufacturers can reduce dependence on a single supplier by diversifying their supplier base. This helps mitigate risks associated with raw material availability and price volatility.
Vertical Integration
Vertical integration involves owning and controlling multiple supply chain stages, from raw material extraction to battery assembly. This strategy provides greater control over costs, quality, and supply chain stability.
Investment in Research and Development
Continuous investment in research and development is crucial to improve battery performance, reduce costs, and enhance supply chain efficiency. Innovations in battery chemistry and manufacturing processes can significantly impact the economics of lithium battery production.
Future Outlook for Lithium Battery Production and Supply Chains
The future of lithium battery production and supply chains looks promising. As technology advances and economies of scale are achieved, the cost of lithium batteries is expected to decline further. Increased investments in renewable energy, electric vehicles, and energy storage systems will continue to drive the demand for lithium batteries, fostering the industry’s growth.
Conclusion
The economics of lithium battery production and supply chains are complex, influenced by various factors such as raw material costs, manufacturing processes, and global demand. Understanding the intricacies of the lithium battery industry is crucial for stakeholders involved in producing, distributing, and utilizing lithium batteries. The sector can overcome challenges and drive further advancements in clean energy technologies by optimizing supply chains, diversifying suppliers, and investing in research and development.
Read More –Â Why Bluetooth Lithium Battery is the Best New Technology
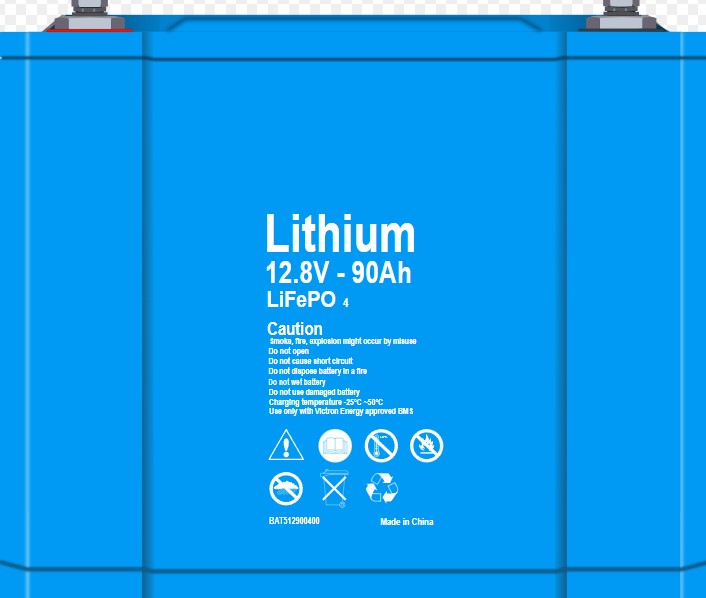